Plastic in construction | A dangerous dependance
In little more than 50 years, plastic materials have become a dominant feature of the built environment, being used to manufacture virtually everything, from pipes and cables to floor coverings, doors and windows.
With its growing dependence on the material, the construction industry has contributed significantly to the rise of plastic consumption globally. However, this reliance is now beginning to raise questions, not only about the environmental impact of plastics but also their implications for human health.
Below, we take a closer look at the increasing use of plastic in construction, the dangers of plastic materials within the built environment and potential solutions for promoting safer, more sustainable construction practices.
The rise of plastic in construction
Read up on the emergence of plastics within construction, the most common types of construction plastics and their different design applications within buildings.
Read MoreThe dangers of plastic in construction
Learn about the key issues associated with the use of plastic in construction, including fire safety, environmental pollution and leaching of microplastics.
Read MoreAlternatives to plastic in construction
Find out what needs to be done to reduce the construction industry’s plastic problem and discover other materials that offer a healthy alternative to plastic.
Read MoreThe rise of plastic in construction
While some of the first plastics were synthesised as early as the 1870s, it wasn’t until the 1930s and the introduction of new manufacturing techniques that modern synthetic plastics started to emerge.
By the 1950s, the global plastic industry was beginning to take shape, with production rapidly increasing on a trajectory that has not slowed since.
Already at this stage, the construction industry had emerged as one of the biggest consumers of plastic. By 1960, polyvinyl chloride (PVC) plastic was being used extensively for water service lines in Japan, Italy, Germany and the Netherlands.
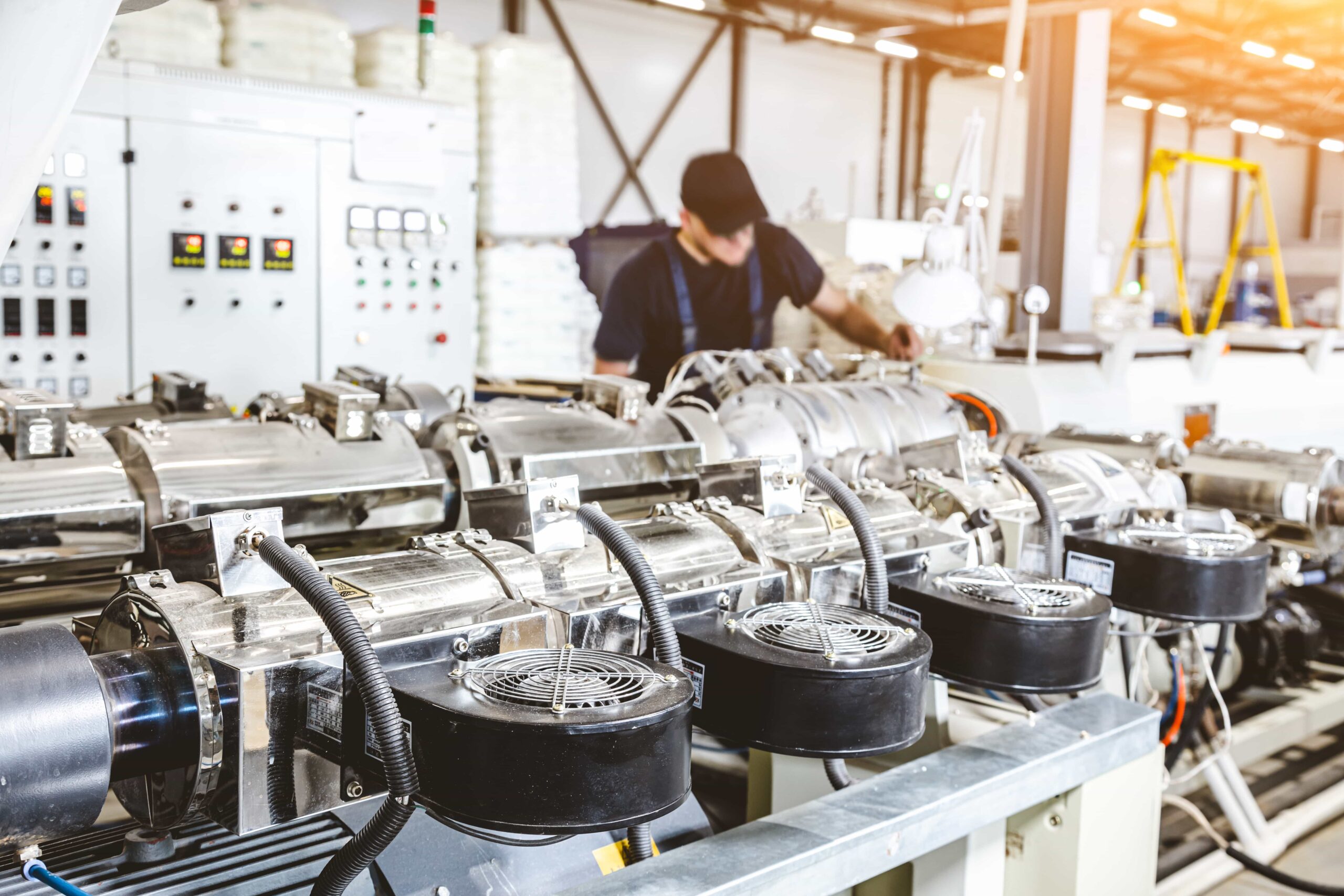
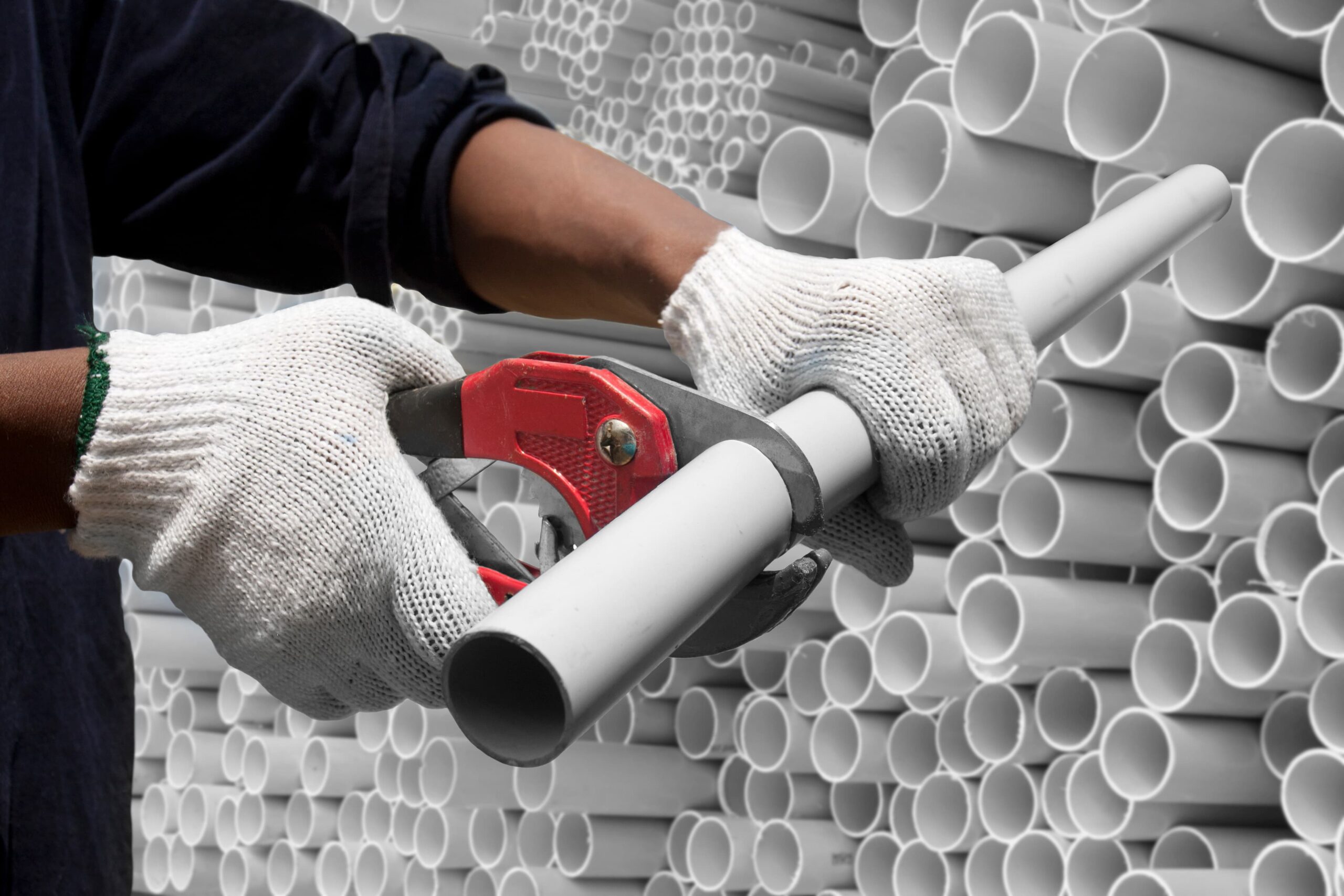
Elsewhere, building insulation made from polystyrene (PS) plastic was being used in walls, roofs and foundations. Polypropylene (PP) plastic also emerged around this time, giving rise to the use of plastic in drainage systems and roofing panels.
Between 1950 and 1970, global plastic production increased twentyfold to 35 million metric tons. By 1990, this figure had more than quadrupled to 130 million. Two decades later, in 2010, global production had reached 313 million metric tons.
The amounts used have grown exponentially, with the construction industry continuing to be one of its primary proponents. In 2019, the industry consumed around 77 million metric tons of plastic, accounting for 17% of global plastic production and ranking second only to the packaging sector.
Which plastics are used in construction?
Since its inception, the plastic industry has worked continuously to develop new materials with different sets of properties. Today, the most common plastics in construction are:
- Polyvinyl chloride (PVC)
- Polyethylene (PE)
- Composites
- Polycarbonate (PC)
- Polypropylene (PP)
PVC
PVC is primarily a building material, with the construction industry responsible for around 60% of global demand.
Versatile and lightweight, PVC is used to produce a wide range of construction fittings, including pipes, cables, flooring, windows and roofing.
PE
Another commonly used plastic building material is polyethylene (PE), which includes several variations like high-density polyethylene (HDPE) and low-density polyethylene (LDPE).
PE is a key component in cross-layer polyethylene (PEX) and multi-layer composite (MLCP) pipes and can also be used to make cladding panels and roofing sheets.
PC
Polycarbonate (PC) is a type of thermoplastic that has become increasingly common in building and construction projects.
PC panels are transparent, making them a popular choice for exterior design elements like windows, skylights, cladding and roofing.
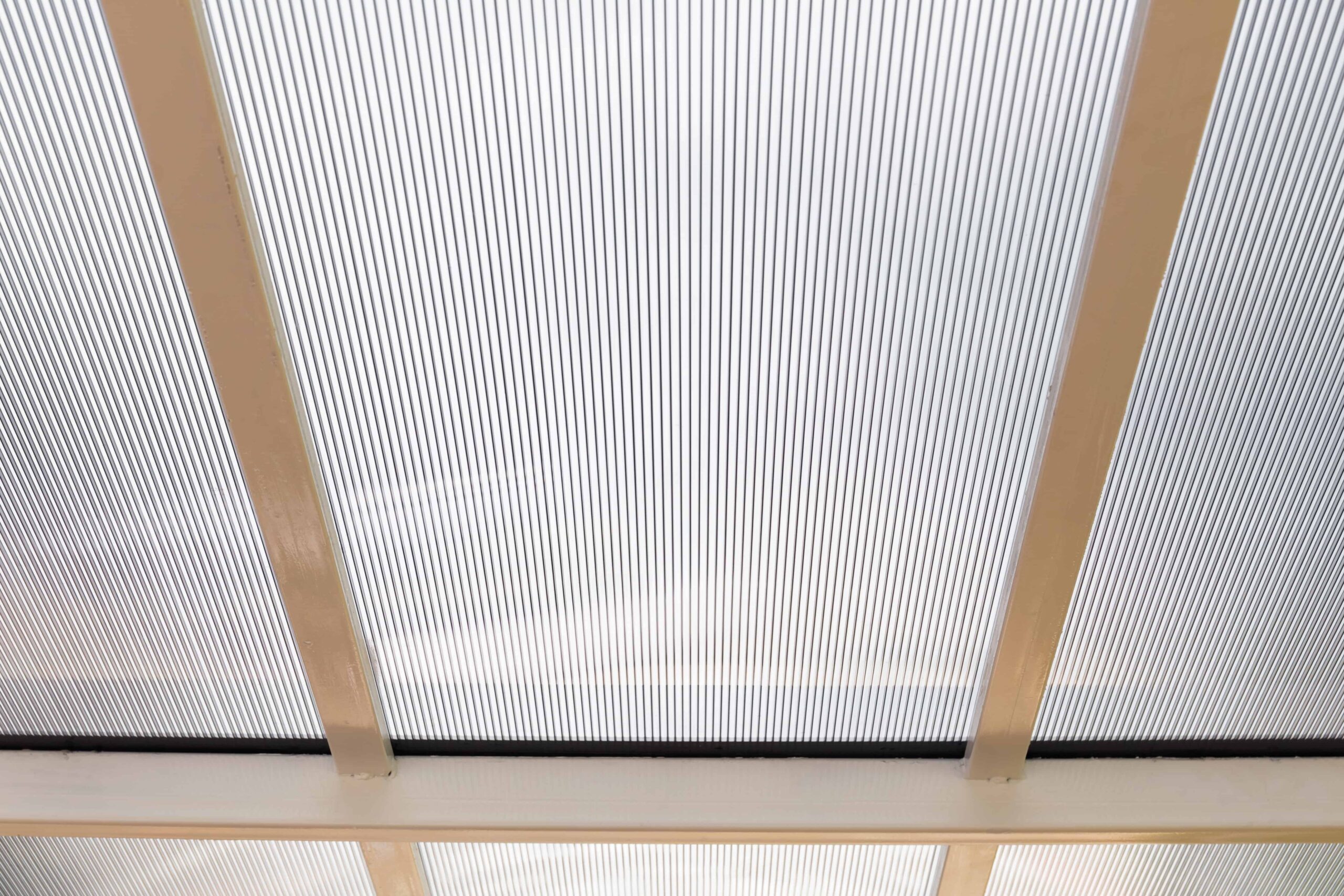
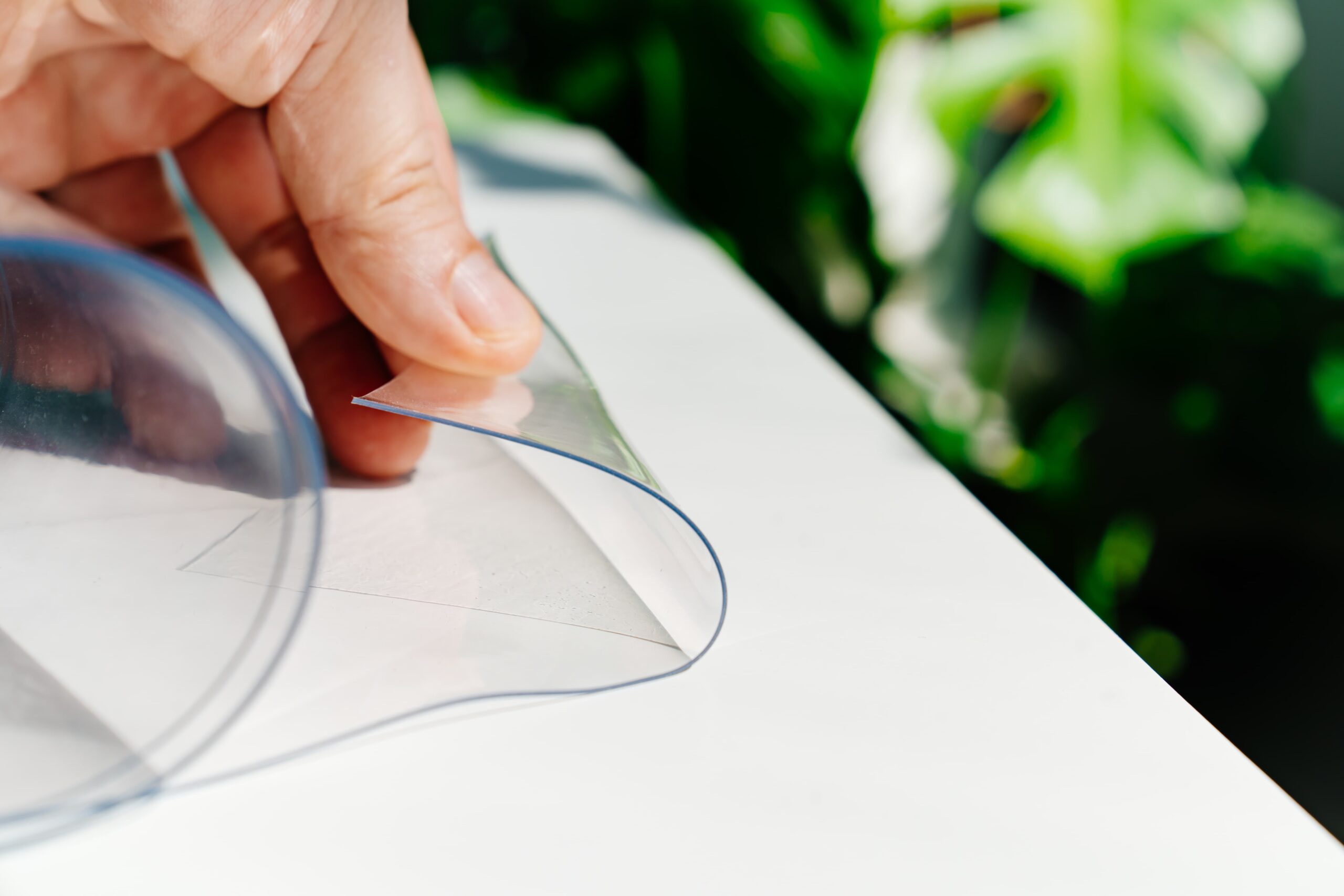
Composite
In many cases, plastics are bonded together or combined with entirely different materials to form composites with superior properties.
Some of the most common plastic composites used in construction are aluminium composite material (ACM) and fibre-reinforced polymer composite (FRP).
PP
After PE, PP is the most widely produced plastic in the world. While primarily used for packaging, PP can also be found across the built environment.
Common construction applications for PP include carpeting, piping systems, roofing sheets, building insulation and electrical cable insulation.
What are the uses of plastic in construction?
Initially used in piping systems and insultation, plastic materials have come to dominate virtually all aspects of building design. Some of the main uses of plastic in construction today are:
- Pipes
- Roofing
- Flooring
- Insulation
- Cladding
Pipes
One of the most common uses of plastic in construction is piping, with the material used to manufacture pipes for plumbing and heating as well as drainage.
Plastic pipes in domestic settings are generally made with PEX and PVC, however composites like MLCP can be used too.
Roofing
Corrugated plastic sheets are often used in roofing, providing a basic form of protection for outdoor sheds, greenhouses and conservatories, as well as many industrial buildings.
Plastic roofing sheets are generally made from PP or PVC, serving as a cheaper alternative to traditional roofing tiles and glass panels.
Flooring
Another area is which plastic has become increasingly common is flooring, with plastic floor coverings emerging as an alternative to materials like wood and carpet.
Several different types of plastic are used within the flooring industry, including PE, PP and PVC.
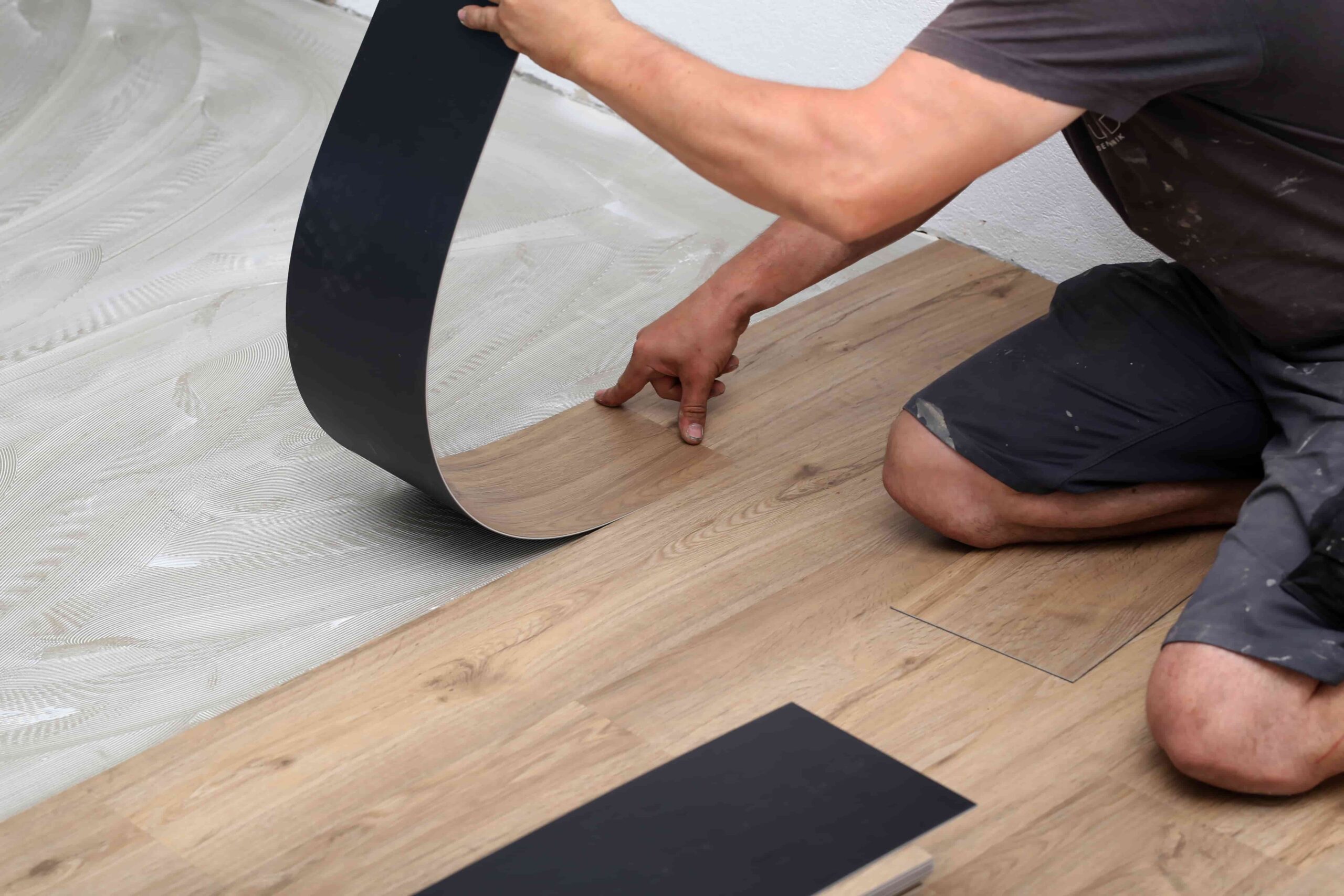
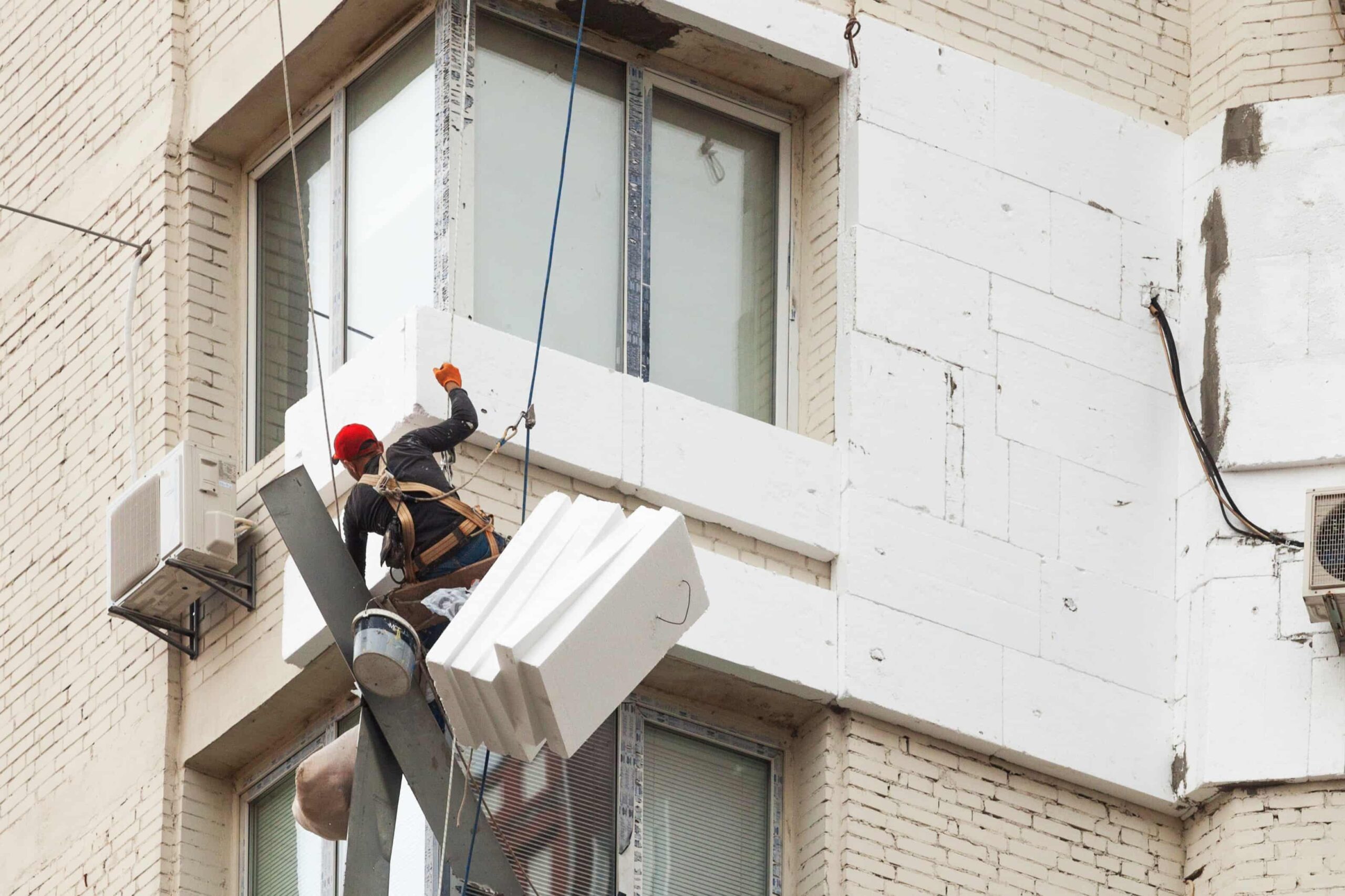
Insulation
Foamed plastic materials are often used to insulate the floors, ceilings and walls of commercial and residential buildings.
Expanded polystyrene (EPS) and extruded polystyrene (XPS) are generally used for insulation along with other plastics like polyurethane (PUR) and polyisocyanurate (PIR).
Cladding
Plastic cladding sheets have become another common feature of modern buildings, often being fitted onto external walls for protection from outside elements.
There are many different types of plastic cladding panels, with some of the most common materials being PVC, PP and ACM.
Learn more about the rampant rise of plastics in society
The dangers of plastic in construction
The prevalence of plastic in construction is largely due to its relatively low cost and ease of installation. Today, plastic materials are routinely used in new builds and renovation projects where only a matter of decades ago other materials would have been specified as standard.
However, the construction industry’s relationship with plastic is now presenting problems. In many cases, plastics do not perform as well as the materials that they have come to replace, while they also pose considerable risks to the environment and human health.
Poorer quality buildings
In spite of the claims made by the plastic industry, synthetic materials are generally found to be less durable than traditional building materials like glass, metal and concrete. This is because they are structurally weaker, rendering them more vulnerable to degradation and eventual failure.
Many plastic manufacturers state that their products will last decades with minimal maintenance, but in reality there is little evidence to support these claims, not least because most plastic materials have not yet been around for long enough to test the supposed service life of the product.
Where robust data has been collected, the evidence shows that plastic building products often cause problems for occupants. For instance, research from the UK insurance industry links the use of push-fit plastic plumbing fixtures with an increase in escape of water claims.
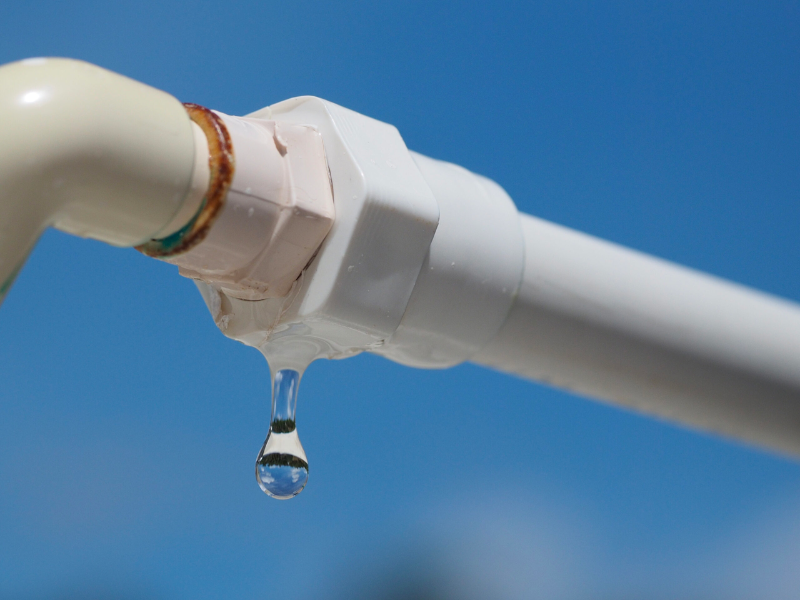
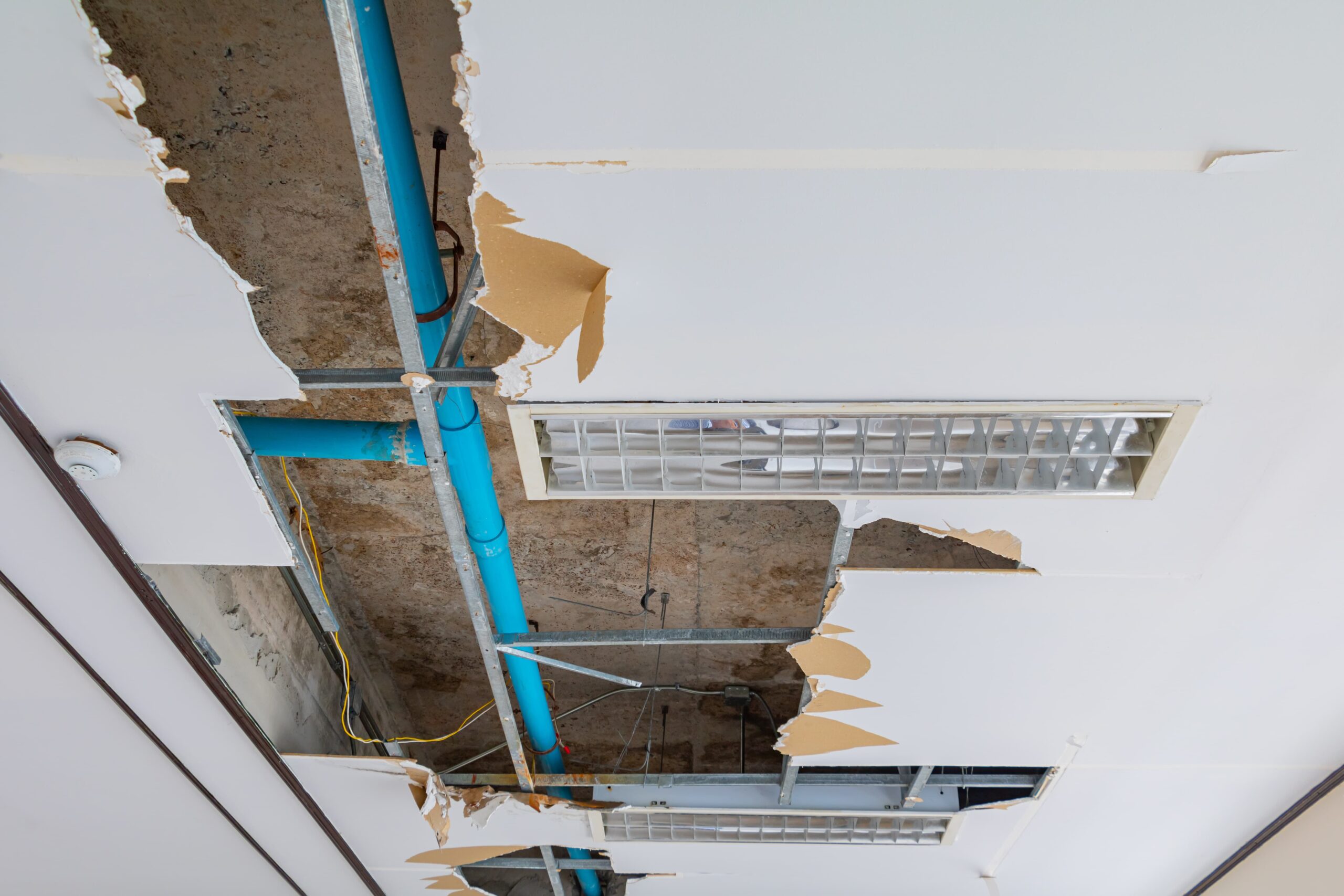
With time, the combined effects of prolonged exposure to heat, oxygen and UV radiation cause plastics to become brittle, eventually leading to breakages and incurring extra costs for property owners.
It’s no surprise that new-build homes — with which plastic construction materials have become synonymous — are deemed of poorer quality than older homes made with more traditional building materials by respondents in a survey by the Chartered Institute of Building.
So, while plastics can help save costs during installation, they may ultimately prove more expensive across the service life of a building, requiring extra maintenance and earlier replacement than more durable, longer-lasting materials.
Learn more the design flaws of plastic pipes below
Fire safety risks
Most plastics used in construction are derived from petroleum products like crude oil and natural gas. As such, they are naturally flammable and will burn when subjected to an ordinary flame.
To mitigate against these risks and comply with building codes, plastic construction materials are usually treated with flame-retardant additives prior to installation, though in many cases these chemicals may only delay ignition by a few seconds.
The San Antonio Statement, signed in 2010 by representatives from 30 countries, concluded that the fire safety benefits of brominated and chlorinated flame retardants had not been proven, while also noting that the chemicals used in these products had hazardous properties.
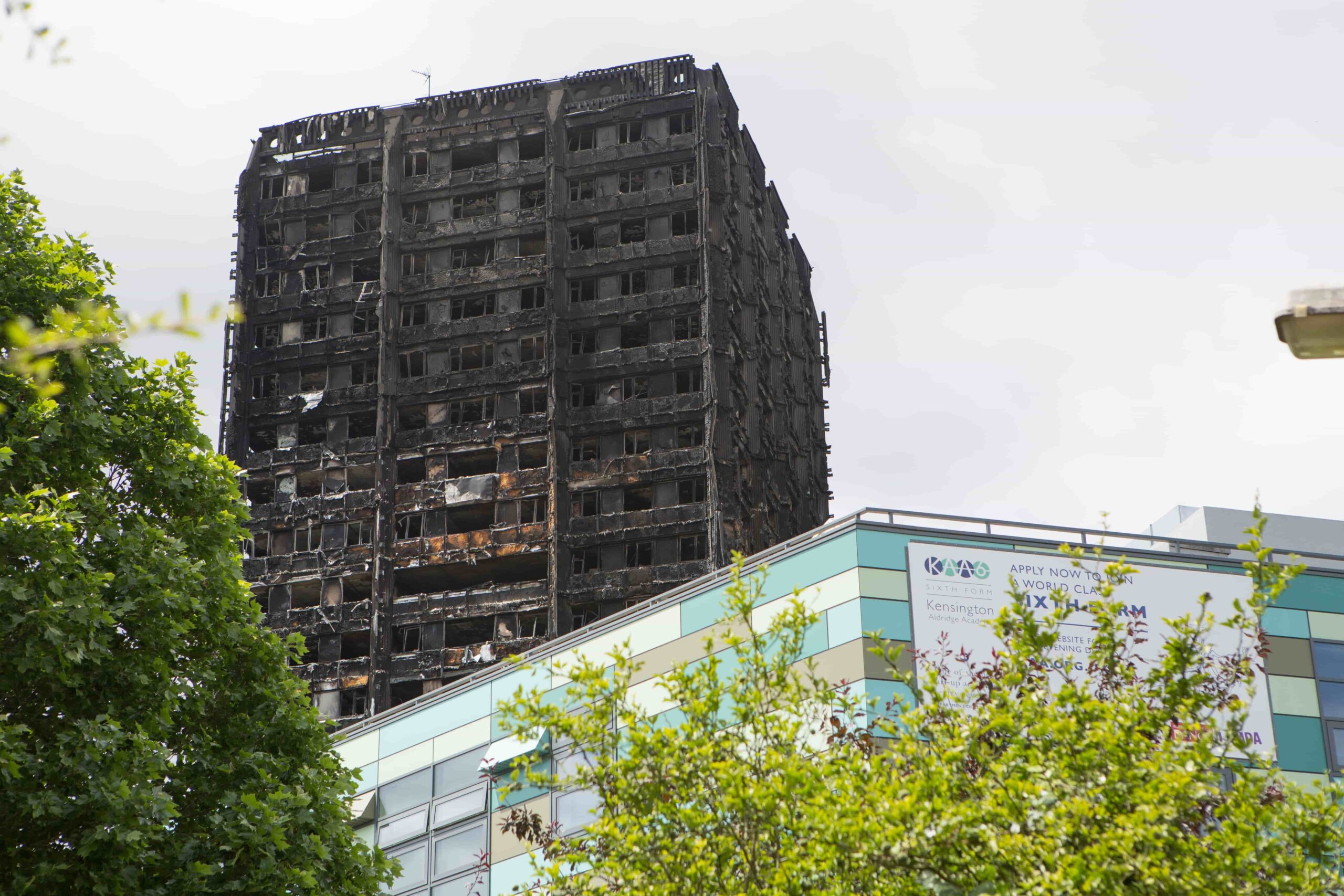
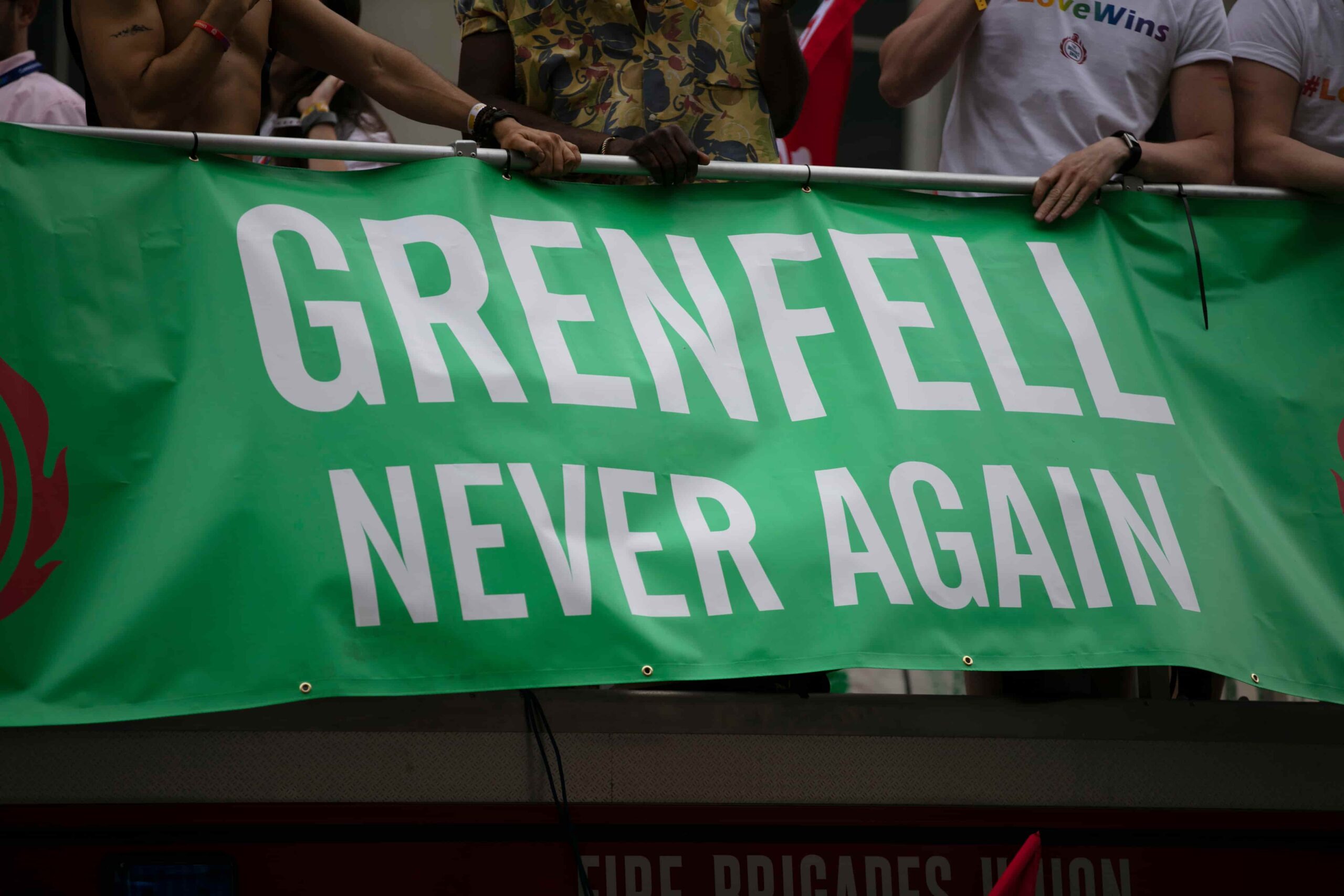
A number of fires in recent history have been directly linked to burning plastic, with one of the most well-known examples being Grenfell Tower. Inquiries into the fire described the ACM cladding used in the facade as ‘the primary cause’ of the fire spreading, with one study finding the panels to be 55 times more flammable than the least combustible materials available.
Not only do burning plastics accelerate the spread of a fire, but they also release highly toxic chemicals in the process. These include sulphur dioxide, hydrogen chloride acid and volatile organic materials, as well as furans, dioxins and heavy metals.
Several years on from Grenfell, it was revealed that a dozen firefighters involved in the incident had been diagnosed with terminal cancer, likely a result of the exposure to toxic smoke they faced on the day.
In the US, research into the toxicity levels of the water supply following wildfires in California in 2017 and 2018 found that thermally degraded plastic pipes had leached dozens of dangerous chemicals into drinking water.
Learn more about the fire safety risks of plastics below
Harmful to human health
A huge range of colourants, fillers and reinforcing materials are used in the manufacture of plastic products to enhance their properties. Many of these additives are yet to be tested, and of those that have been, an alarming number have been identified as harmful.
In 2021, an analysis of more than 10,000 additives routinely used in plastic manufacturing found over 2,400 substances that were considered substances of concern in line with the EU’s criteria for assessing the toxicity of chemicals.
In many cases, these substances do not need the fuel of a fire to leach out into the environment. One study found that as much as 88% of the chemicals used in everyday plastic products were released during regular use.
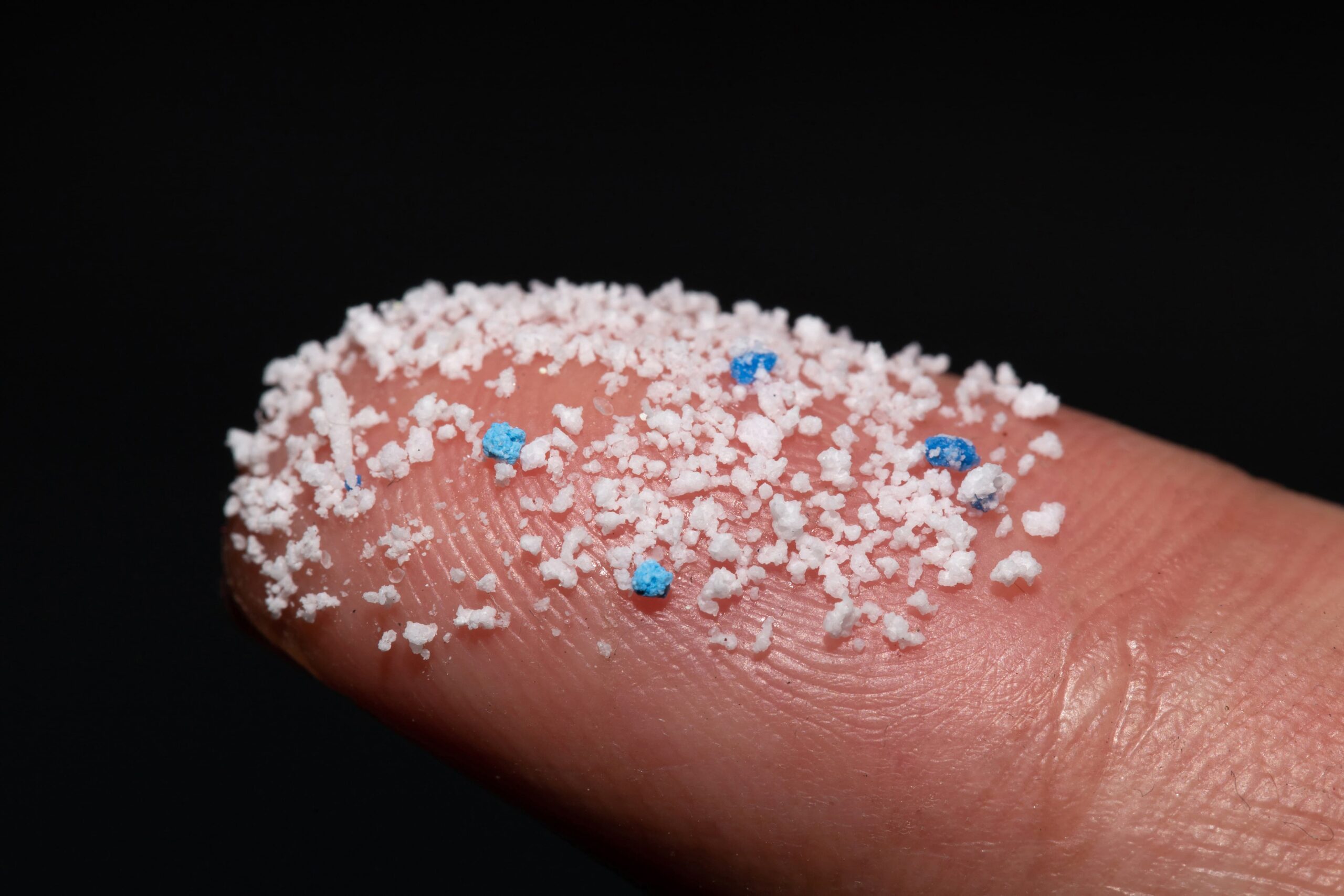
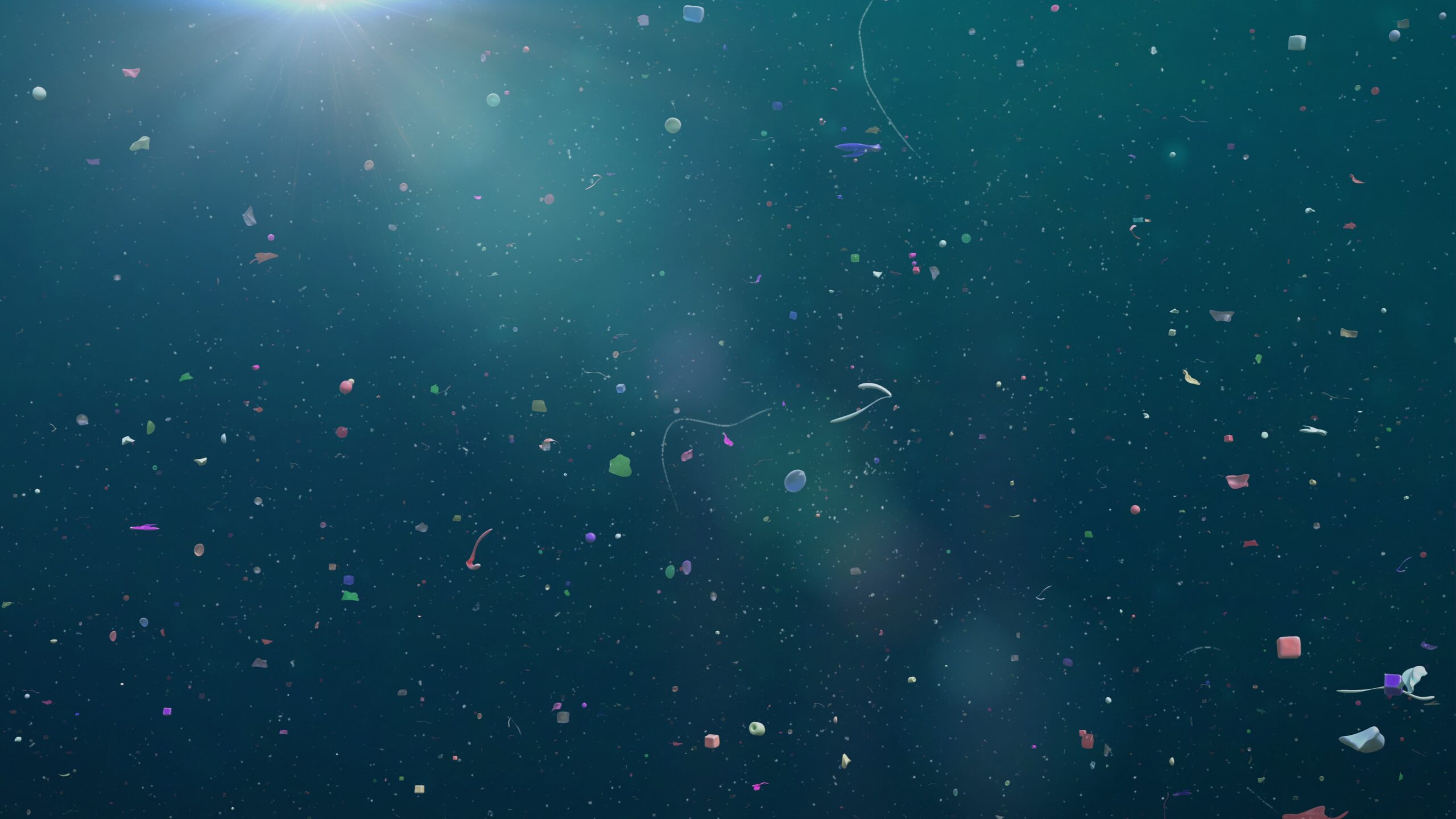
This news is especially concerning considering plastic pipes are used to supply drinking water in many new-build homes, with one studying finding that both PE and PVC pipes release tiny particles into water when they crack and peel.
Plastic pipes can therefore significantly increase exposure to harmful microplastics, which have been linked to a wide range of serious health problems including oxidative stress, organ dysfunction and weakened immune response.
The body of evidence highlighting the risks of plastics for human health is building up rapidly, now approaching a similar scale to previous public health crises with lead and asbestos.
Learn more about the health risks of microplastics below
Damaging for the environment
One of the more well-documented issues with plastics is their environmental impact. Construction plastics generally have a shorter service life than traditional building materials, with the increased maintenance that comes with plastic building products equating to increased energy consumption.
Not only does plastic lack the longevity of a truly sustainable material, but it is also rarely recycled. In spite of the sustainability claims made by the plastic industry, only 9% of plastic ever produced has been recycled.
When a plastic product reaches the end of its lifecycle, it’s likely to either be incinerated, sent to landfill or simply left to leach into the environment, contaminating food and water sources with harmful microplastics.
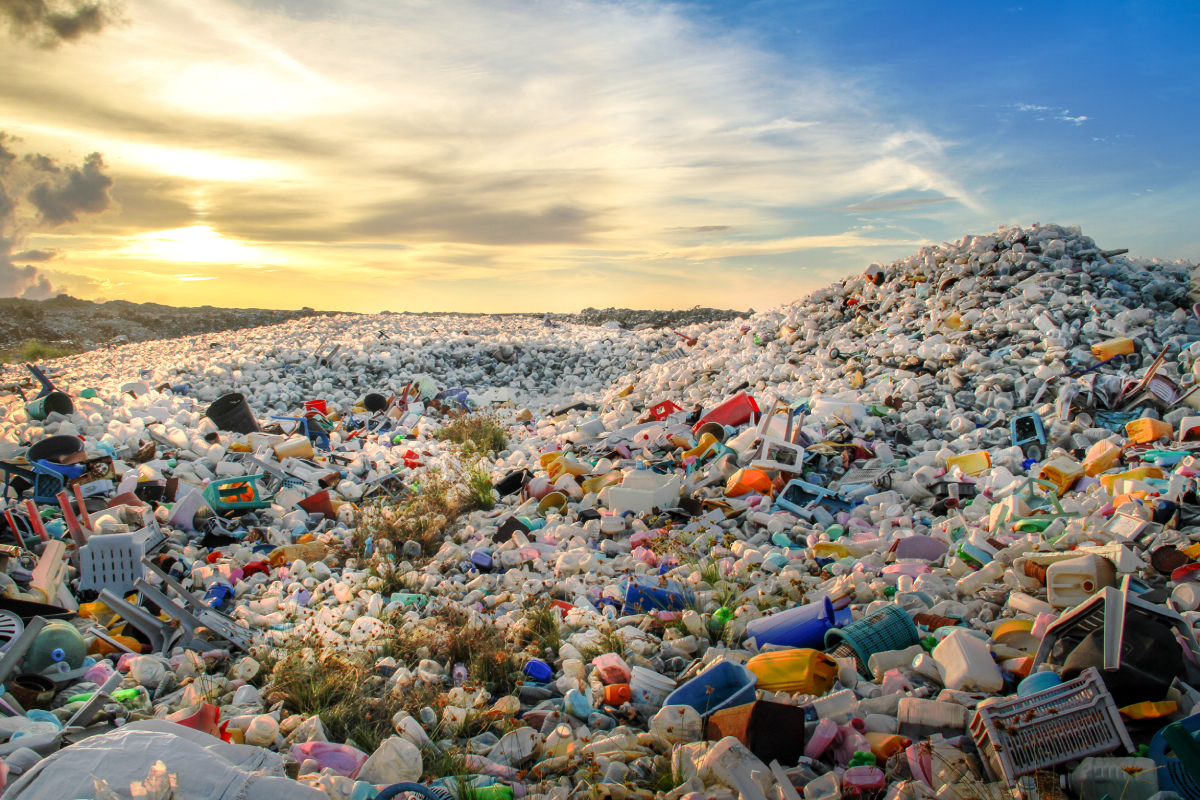
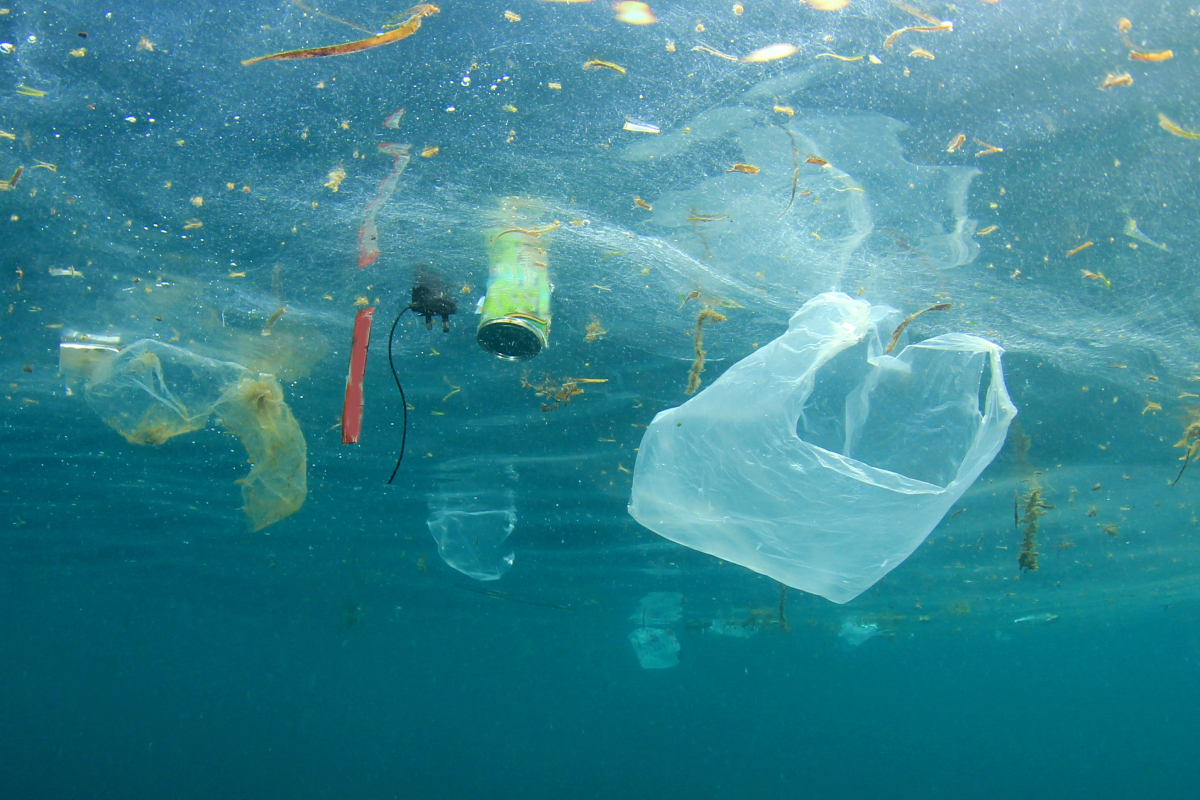
The reason why plastic recycling rates are so low is because plastic materials are inherently difficult to recycle. Some plastics simply cannot be recycled, and those that can must firstly be separated as part of a process that is incredibly expensive and time-consuming.
These reasons render the vast majority of plastics single-use, despite existing recycling processes, particularly as costs for the raw materials needed to produce virgin plastics often come in cheaper.
Critically, when recycling does occur, the properties of the recycled plastic are altered in a way that reduces its quality, which means the residual material does not meet the same quality of the product that was recycled.
For this reason, plastic can only be recycled a handful of times before it becomes completely unusable, meaning it has no part to play in the circular economy.
Chemical recycling has long been pushed by the plastic industry as a solution to this problem, however there is little evidence to suggest that this so-called advanced method of recycling is actually successful nor that it can ever happen at scale.
Learn more about the impracticalities of plastic recycling below
Alternatives to plastic in construction
The construction industry’s reliance on plastic is one of the main barriers to a sustainable future for the sector, with the material’s increasing usage also introducing unnecessary safety risks and leading to poorer quality buildings.
While some changes are beginning to take shape, such as the UK government’s ban on Grenfell-style PE cladding, building codes in most countries still fail to account for the dangers and design limitations associated with construction plastics.
As a matter of urgency, more needs to be done to identify excessive use of plastic in areas where the risks to human health are high, such as plumbing systems that carry drinking water or building components that represent a fire hazard like walls, doors and cladding.
While improved standards can help make the use of construction plastics safer, the most effective method of reducing their impact would be to limit their applications in favour of more natural materials with proven safety credentials.
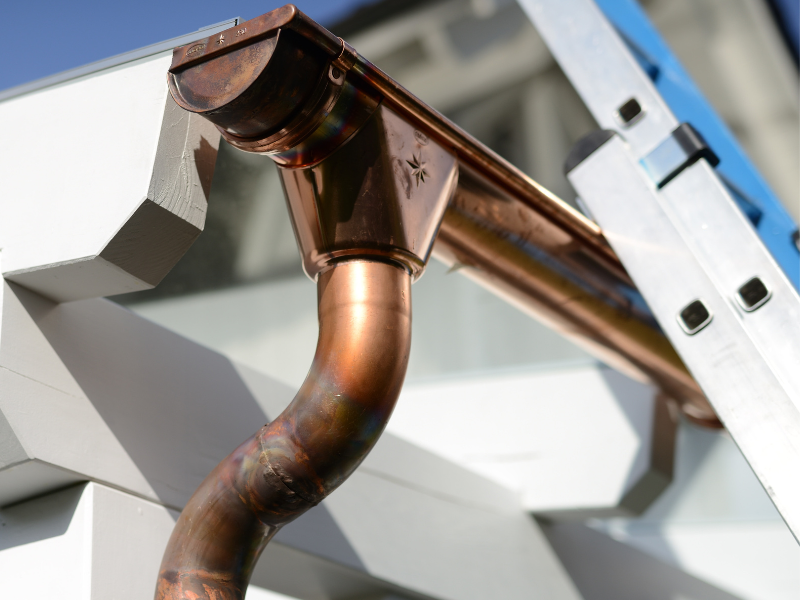
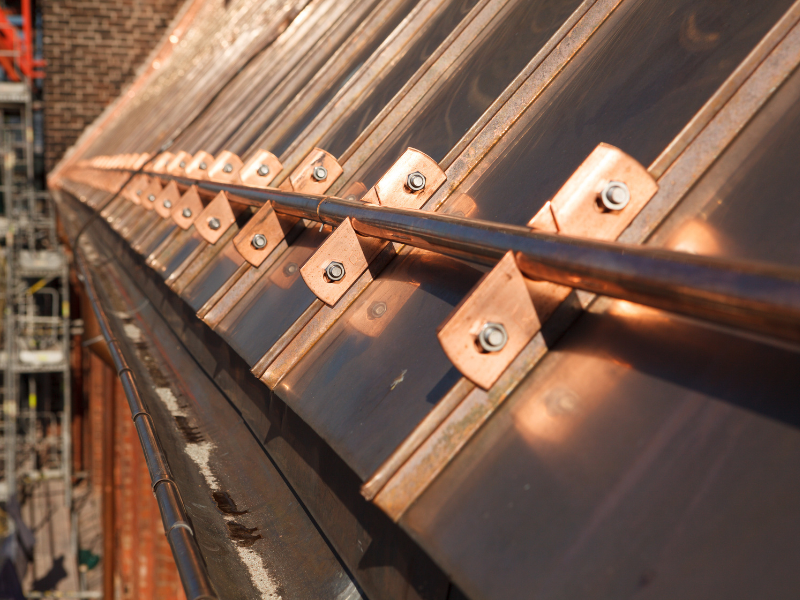
With piping and guttering, metals like copper, steel and cast iron are more durable than plastic pipes and can also be infinitely recycled. What’s more, they have much higher melting points than plastic, making them naturally resistant to fire.
In the case of copper, the metal is also naturally antimicrobial, possessing a unique ability to eliminate bacteria, viruses and fungi that land on its surface. It’s one of the many reasons why copper pipes have been used for centuries to safely transport water.
Elsewhere, timber and aluminium serve as two healthy and sustainable alternatives to plastic for doors and window panels. With insulation, cellulose, wood fibre and wool are all natural substitutes for commonly used polystyrene rolls.
In many cases, these materials have been in use long before the introduction of plastics in construction. It is largely through cost considerations they have come to be replaced, however with hindsight it has become clear that they are better equipped for the job than plastic.
Learn more about the use of copper as an alternative to plastic below
Plastic in construction: an unhealthy relationship
In spite of the growing amount of research into the potential dangers of plastics, the construction industry’s use of the material is expected to continue growing exponentially over the coming years, further escalating many of the problems we are already seeing in the built environment.
As researchers work to fill in the gaps in knowledge surrounding the health risks of plastic, there is already enough evidence to support the view that the material’s usage should be limited, particularly in high-risk areas of building.
Fortunately, a wide range of alternatives like copper are readily available. Not only are these materials capable of performing better than construction plastics, but they also eliminate many of the associated health risks and support a circular economy within the trades.
Want to learn more about the role of copper in shaping a safe and sustainable future in the construction industry? Check out some of our related articles or subscribe to our newsletter below.